EDITOR’S NOTE: The following is the first chapter to a book I have not completed. Quite frankly, I’m not sure anyone would want to read the whole book. As such, let me know what you think. Should I push ahead?
Stave I
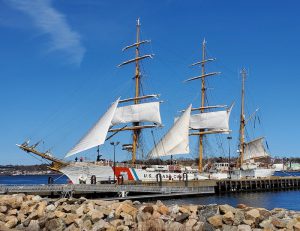
This photo has nothing to do with the story, but didn’t a certain Transylvanian count arrive in London on a ship like this?
Cheers erupted in the operating room when Dr. Tepes removed his bloody hands from the chest of a morbidly obese man. The man’s heart had just restarted after one of the most masterful quadruple bypasses ever performed.
“That was inspiring,” said a young surgical resident. “How on earth did you know you’d find a suitable vein in his calf? His arteries were as congealed as the grease trap at an abandoned McDonald’s”
Dr. Tepes gave a wan smile and tried not to belie his boredom when he explained, “When you have has much experience as I’ve had, sometimes a body just talks to you. Besides, I’ve known this gentleman for several years in town and knew he was an athlete in younger years and suspected there might be additional clear veins in his lower extremities.”
The resident looked on in awe. “Yes, but he came in unexpectedly off an ambulance in cardiac arrest. To think that quickly and remember that well on your feet….”
Even the attending surgeon with 15 years of cardiac surgical experience was impressed. “Sir, that was the most incredible surgery I’ve ever watched.”
“Thank you, Joel,” Dr. Tepes said with warm friendly familiarity. “You really are one of the best cardiac surgeons I’ve ever worked with. That means a lot.”
The nurses agreed and complimented.
“Dr. Brown, do you mind closing him back up and putting the finishing touches on our patient?” Dr. Tepes asked.
“It would be an honor, Sir,” replied the resident.
“Great. It’s 2 a.m., and I’m more than a little hungry for a much delayed lunch break.”
“I’ll keep a close eye on young Brown,” Dr. Joel Irving replied. “I’ll catch up with you to go over the surgery for our notes when we’re done.”
Dr. Tepes thanked Dr. Irving wearily with a pat on the upper arm, as he passed him to head to the hall for his lunch.
Out of his scrubs and into his shirt, tie and white coat, Dr. Tepes listened to the echo of his comfortable gleaming black wingtips, as he walked down the tiles to what he darkly and privately referred to as his lunchroom. His office on the top floor was locked, and everyone assumed he was deep inside enjoying his private meal in solitude, as was his wont. He owned Lucy Westenra Memorial Hospital and only practiced surgery for fun, to keep his hand in the proverbial game. While he likely was the most talented cardiac surgeon on earth, he kept a low profile. He was a quiet soul who didn’t seek out fame or attention. He ran the hospital as a nonprofit to benefit the town of Sleepy Hollow, New York. Some insanely rich executives and movie stars knew of his talents, and they paid a fortune to improve their own lives and essentially fund the hospital for the community.
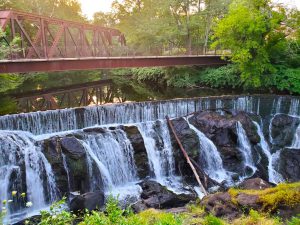
Uncas Falls in Norwich, Conn.
What bothered Dr. Vladislav Tepes wasn’t money or debt, it was shear boredom. A person’s heart and blood spoke to him in ways no one alive could understand, and it was no challenge at all to save a person’s life from cardiovascular problems or gunshots. He set out long ago to try to make amends for his past by saving lives, but he wasn’t even sure it was worth it any more. So few people changed their own lives afterward. So few dedicated their new lives to others or making the most of their own lives. Text books might one day be written about the surgery he just performed, but to him it was so rote that he almost fell asleep about three quarters of the way through it.
In his lifetime, he had seduced every size, color and shape of woman and man. For the past couple decades it was so beyond tedious, messy and boring that he didn’t even bother…or miss it.
He raced cars, flew airplanes, sailed around the world, partied with celebrities, mastered several languages, played several instruments and explored many hobbies from horology to horticulture.
Dr. Tepes looked like he was in his late 40s, but his family had long since passed away. He was stoutly built, and his pale skin and raven-black hair combed from right to left gave him a more youthful look, while his dark eyes and thin lips seemed to age him a little.
Outside of work, he had few friends. People were so predictable. By the time people got interesting to him, they died of old age.
Arriving at a glass-windowed door that said “Hospital Lab,” Dr. Tepes sighed with relief and entered. It was vacant at this hour, so he left out the lights and grabbed a large Pyrex measuring cup—filling it with all of the day’s leftover test tubes of already tested blood. He put the empties in the autoclave and put the cold, congealing mess in the microwave for 40 seconds to get it up to 98.6 degrees Fahrenheit.
***
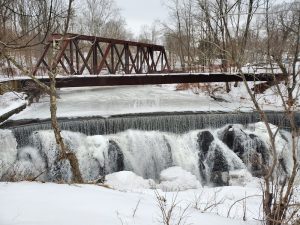
Uncas Falls in Winter. Norwich, Conn.
Dancing down the hallway with his mop and wheeled bucked, few people loved their job as much as José Monterrey. José was the head janitor at Westenra Memorial. A happily married father of three, at 45, José felt like he was on top of the world. He had grown up poor in the rough border town of Juarez, Mexico. Through hard work and good fortune he came to the United States and became a naturalized citizen.
He looked past the petty racism of so many non-Hispanic Americans, focusing on the goodness of many other Americans and the opportunities available to his children that he barely dreamed possible at their age.
Unlike the jobs his parents had to do to get by, keeping a hospital sterilized and safe for patients and co-workers felt simple. Keeping his staff motivated and happy was likewise easy. Westenra Memorial paid top dollar for every employee and offered as strong a benefits package as he’d ever seen for what would normally be low-wage manual laborers.
“Lose a finger, get two free,” he’d joke to his prospective employees.
Only his wife protested.
“José, why don’t you go to day shifts and spend more time with us at home?”
He’d explain, “Rosie, it is so much quieter at night, and I can get so much more done. Plus, they need me there. The nurses and doctors are so stressed out saving lives, I clown around with them and ease their burdens. Same for some of the patients, who are scared and still awake. It isn’t in my job description, but this place is going to put our kids through college. Maybe they’ll be doctors here one day. It is important to give them everything I can.”
He smiled as he thought about his Rose. He twirled around his bucket and mop, pretending to dance with her as he made his way to the last room he needed to clean.
José had strict orders to stay out of the hospital lab when the lights were on or from midnight to 2 a.m., so he saved it for last.
It surprised him a little that the door had been left unlocked at a quarter to 3 in the morning, but the lights were out and people forgot to lock up all of the time.
The tall, athletic janitor flicked on the lights and gasped in horror when he saw the owner of the hospital drinking human blood from a glass bowl.
Dr. Tepes hissed in anger, bearing sharp, elongated fangs at the intruder.
José fell to his knees crying and begging. “Oh, please don’t kill me. I didn’t know! Nobody knows. I won’t tell anyone. I have a wife and children. Please, I’ll do anything you want. Just let me live.”
Dr. Tepes rushed to him with supernatural speed.